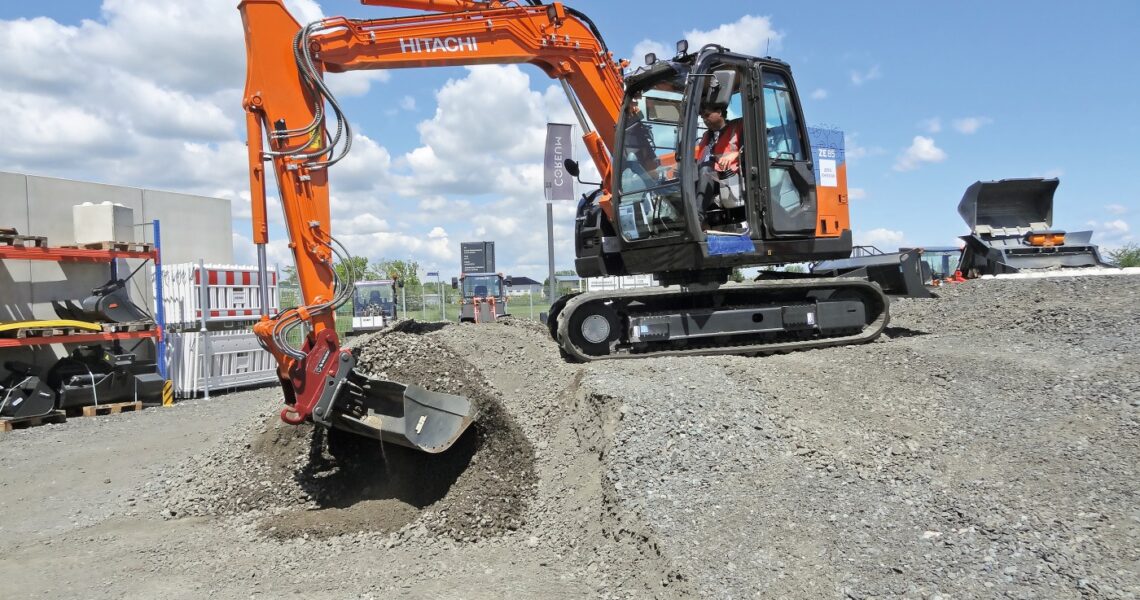
KTEG 9-t-Elektrobagger ZE 85
Auf der Bauma 2019 führte die Kiesel-Tochtergesellschaft KTEG ihren Prototyp eines batteriebetriebenen 9-t-Baggers vor. Jetzt geht er in Kleinserie und wird im Coreum in Stockstadt präsentiert. Dort haben wir den Stromer getestet.
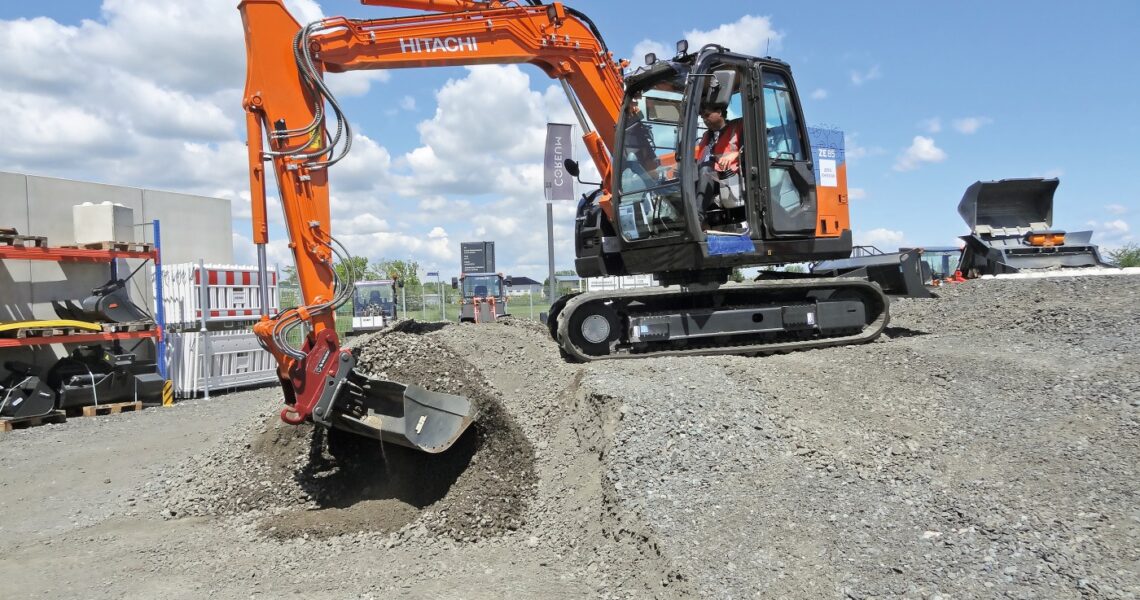
Fast jeder namhafte Baumaschinenhersteller hat mittlerweile einen oder mehrere Elektrobagger auf Messen gezeigt. Wenn es um den realen Einsatz oder die Verfügbarkeit in Mietparks geht, wird die Luft schon dünner. Die KTEG macht nun Nägel mit Köpfen und fertigt den ZE 85 in einer Serie von zunächst 50 Stück. Dazu werden Hitachi-Zaxis 85 US auf Akku-Elektroantrieb umgerüstet. Wurden anfangs noch komplett montierte Bagger umgerüstet, liefern die Japaner heute nur noch die tatsächlich benötigten Komponenten als Umbau-Basis. Die Umrüstung erfolgt in Kooperation mit der Schweizer Firma Suncar HK, die bereits Erfahrungen mit der Elektrifizierung von Mini- und Kompaktbaggern gesammelt hat. Die verbauten E-Komponenten werden bislang vorrangig in Nutzfahrzeugen verwendet.
Das Bauma-Gerät wurde nach Norwegen geliefert und hat dort mehrere tausend Betriebsstunden abgeleistet. Die dabei gewonnenen Telemetrie-Daten waren außerordentlich wertvoll für die Auslegung der Speicherkapazität der Batterie. Betriebsstunden werden bei einem Elektro-Antrieb weitaus differenzierter als üblich betrachtet, für die Akku-Laufzeit zählt ausschließlich die Leistungsaufnahme der Hydraulik und der Peripherie. Einen im Standgas vor sich hin tuckernden Bagger gibt es bei der E-Version natürlich nicht mehr.
Der erste Eindruck
Dass sich die Maschine von der Diesel-Version auch optisch abhebt, ist durchaus erwünscht und wird durch blaue Beklebungen bewusst hervorgehoben. Um die erforderlichen Komponenten im Oberwagen unterzubringen, musste er um 30 cm verlängert werden. Aufgrund der letztlich überschaubaren Seriengröße wurde auf aufwendige Tiefzieh- oder GFK-Verkleidungen verzichtet. Das kostspielige Innenleben wird von gekantetem Blech umhüllt – eine robuste, baustellengerechte Lösung.
Die Konfiguration mit einem neben der Kabine montierten Monoblock ist hierzulande eine eher selten anzutreffende Variante in dieser Baggergröße. Neben einsatzspezifischen Vorteilen – beispielsweise ein geringer vorderer Schwenkradius – hat man genau diese für den Umbau gewählt, weil der Raum für den Zylinder des Schwenkbocks dringend zur Unterbringung der Hydraulikkomponenten benötigt wurde. In der Tat herrscht drangvolle Enge im Inneren, sind es doch ein paar mehr Bauteile, die für so eine Hochvolt-Anlage verbaut werden müssen.
Der Li-Ionen-Akku mit NMC-Technologie ist je nach Anforderung in verschiedenen Kapazitätsstufen erhältlich. Der Hersteller gibt die erwartete Lebensdauer der Batterie mit 8.000 bis 10.000 Betriebsstunden an. Der eigentliche Elektromotor beansprucht erstaunlich wenig Raum – er hat etwa die Abmessungen eines Sonnenschirmständers. So unscheinbar er aber auch daherkommt, seine Daten sprechen eine eigene Sprache: So ist das maximale Drehmoment mit 400 Nm um satte 70 Prozent höher als beim Diesel-Pendant. Soviel zum Thema Hubraum. Der E-Motor ist durch eine Kupplung mit der Hydraulikpumpe verbunden; von der Anordnung mal abgesehen, ist ab hier alles Standard.
Die 800-Volt-Anlage bildet ein in sich geschlossenes System, der Rahmen dient also nicht als Masse, was Kurzschlüssen vorbeugt. Insgesamt sind zahlreiche Sicherheitssysteme vorhanden. So wird die Temperatur der Batterie beim Laden und im Betrieb überwacht. Auch kontrolliert das System ständig die Isolation der Hochvolt-Sektion. Deren orangerote Kabel sollten auch forsche Schrauber davon abhalten, ohne spezifische Fachkenntnisse am System herum zu doktern. Um alle Reparaturen an der Maschine ausführen zu können, erhalten die Werksmonteure eine einwöchige Hochvolt-Schulung. Eine besondere turnusmäßige Prüfung des elektrischen Systems ist nicht erforderlich, der Elektromotor ist wartungsfrei.
In der Kabine
Wie zu erwarten, entspricht die Kabine in weiten Teilen der der Standardmaschine. Lediglich das Display wurde durch einen größeren Bildschirm ersetzt. Neben den üblichen Bedienfunktionen können hier Daten zum Zustand der Batterie sowie des Ladevorgangs abgerufen werden. Um Bedenken gleich entgegen zu treten: Weder auf eine leistungsfähige Heizung, noch auf eine Klimaautomatik muss der Bediener verzichten. Die Batterie muss je nach Betriebszustand gekühlt oder beheizt werden. Diesen Umstand macht man sich zunutze und verwertet die anfallende Energie über eine Zweiwege-Wärmepumpe zur Temperierung der Kabine.
Für den Betrieb des Elektrobaggers sind wiederum keine spezifischen Kenntnisse erforderlich. Da es sich allerdings um ein besonders hochwertiges Gerät handelt, ist er in den Händen eines verantwortungsbewussten Bedieners am besten aufgehoben. Einstellungen, die von der Dieselmaschine abweichen, können lediglich bei der Wahl der Batterieladung vorgenommen werden. Es stehen der aus dem Fahrzeugbereich bekannte CCS2-Anschluss (45 min Ladezeit) oder der in jedem Baustromkasten vorhandene rote CEE-Stecker (105 min Ladezeit) zur Verfügung.
Im Testbetrieb
Dass der Bagger eine ungewohnte Geräuschkulisse erzeugt, überrascht nicht wirklich. Völlig geräuschlos wie manche Elektro-Pkw geht er allerdings auch nicht zu Werke. Der Sound ist vergleichbar mit einer elektrisch betriebenen Arbeitsbühne. Durch den fehlenden Dieselmotor treten die Geräusche der Hydraulik, besonders die der Axialkolbenpumpen, akustisch in den Vordergrund. Das ist gewöhnungsbedürftig, fällt aber nicht unangenehm auf.
Ein Unterschied im Vergleich zum Dieselantrieb bei Kraft und Geschwindigkeit ist nicht feststellbar. Leistung ist eben doch eine physikalische Größe und nicht proportional zu dem Radau, den ein Motor erzeugt. Für die Kommunikation mit dem Bodenpersonal ist der neue Antrieb auf jeden Fall ein großes Plus: Sobald keine Bewegung ausgeführt wird herrscht Stille.
Der nicht vorhandene Schwenkbock ist mir zuletzt stärker aufgefallen als die Tatsache, dass es sich um einen E-Antrieb handelt. Bei dieser Anordnung des Auslegers sind die Sichtverhältnisse eher mit einem ausgewachsenen Kettenbagger vergleichbar.
Die zentrale Frage nach der Laufzeit der Batterie wird bei maximaler Konfiguration mit vier Stunden angegeben. Hierbei spielt naturgemäß die Art des Einsatzes eine große Rolle. Gerade bei ausdauerndem Betrieb im Abbruch, mit Hydraulikhammer oder Abbruchzange, sind über einen längeren Zeitraum oft nur geringe Ortswechsel erforderlich. Der am Heck installierte Stecker ermöglicht bei geschickter Kabelführung ein Nachladen während des Betriebs – was einen zeitlich nahezu unbeschränkten Einsatz ermöglicht. Bei solchen Anwendungen wäre also eine kleinere Batterie ausreichend, mit entsprechend positiver Auswirkung auf die Anschaffungskosten.
Unser Fazit
Das Konzept ist auf jeden Fall interessant. Einer rasanten Verbreitung auf heimischen Baustellen steht gewiss noch der Anschaffungspreis im Weg – er wird derzeit mit dem Dreifachen der Dieselversion angegeben. Mittelfristig wird eine Reduktion aufs Doppelte angestrebt. Allerdings sollten auch die Energie- und Wartungskosten sowie die Lebensdauer der Komponenten in die Kalkulation einbezogen werden. Und hier ist der E-Antrieb auf lange Sicht im Vorteil. Sollten sich die gesetzlichen Rahmenbedingungen oder die Vorgaben in Ausschreibungen künftig ändern, wie es in einzelnen skandinavischen Ländern bereits der Fall ist, könnte der Elektro-Bagger plötzlich zur attraktiven Alternative werden.
Auch hierzulande gibt es bereits Auftraggeber, die innovativen Bauverfahren den Vorzug geben. Zudem würden finanzielle Förderprogramme wie bei der Elektromobilität sicherlich etwas mehr Schwung bringen. Und nicht zuletzt könnte der Weg über die Mietparks ein Einstieg sein, projektbezogen sollten sich die Mehrkosten wieder einspielen lassen.
Dirk Bömer, bd-Baggertester, Wuppertal
„Bei Kompaktmaschinen wird der Elektroantrieb in den nächsten 10 bis 20 Jahren zum Standard werden. Minibagger und -dumper kommen häufig im urbanen Raum zum Einsatz, wo Lärm immer als störend wahrgenommen wird. Zudem führt die bauartbedingt niedrige Anordnung von Auspuffanlagen zwangsläufig dazu, dass sich das Baustellen-Team mit einer Abgaswolke umgibt – unnötig und schädlich. Bei handgeführten Geräten wie Verdichtern, Trennschleifern oder Vergleichbarem wird der Übergang sicherlich noch rascher erfolgen. Die Belastung durch Lärm und Abgas eines hochtourigen Zweitaktmotors war – mal ehrlich – schon immer eine Zumutung. Und da reden wir noch gar nicht von dem aufkeimenden Frust, wenn so ein per Zugstarter angerissenes technisches Machwerk nicht anspringen will.
Die Bauwirtschaft träumt einerseits vom BIM, andererseits werden scheinbar klaglos Arbeitsbedingungen wie zu Zeiten der Frühindustrialisierung hingenommen. Es wäre begrüßenswert, wenn in diese Entwicklung etwas mehr Dynamik käme – auch unter dem Aspekt der viel beschworenen Steigerung der Attraktivität von Bauberufen. Bei allen Einsätzen in geschlossenen Räumen dürfte der E-Antrieb mittelfristig sowieso alternativlos sein.
Die Vorbehalte gegenüber dem Akku-Antrieb nähren sich hauptsächlich aus der bislang eher geringen Verbreitung dieser Technologie. Ein wachsender Markt und verlängerte Batterie-Laufzeiten bei geringeren Anschaffungskosten werden sich gegenseitig bedingen. Häufiges Gegenargument sind zudem fehlende Lademöglichkeiten auf der Baustelle. Nun: Bertha Benz musste den Kraftstoff für den Motorwagen ihres Gatten auch noch in einer Apotheke erwerben. Anfänglich mangelnde Infrastruktur muss also nicht zwangsläufig dem Erfolg eines Konzepts im Wege stehen. Einwände, die das Fehlen eines satten Motor-Sounds betreffen, liegen auf Stammtischniveau und sind wohl auch eher eine Generationenfrage.
Gleichzeitig ist der Batterie-Betrieb auch kein Allheilmittel. Für bestimmte Maschinen-Gattungen und Einsatzbereiche werden wir noch andere Antriebskonzepte erleben. Da die heute gebräuchlichen Hydraulikkomponenten ursprünglich für den Betrieb mit Dieselmotoren konzipiert wurden, stecken in der Abstimmung auf die Charakteristik des E-Antriebs noch große Reserven für den Wirkungsgrad des Gesamtsystems. Eine völlige Abkehr von der Hydraulik wie bei manchen Konzeptmaschinen halte ich jedoch bei den gegebenen Einsatzbedingungen für eher unwahrscheinlich.“