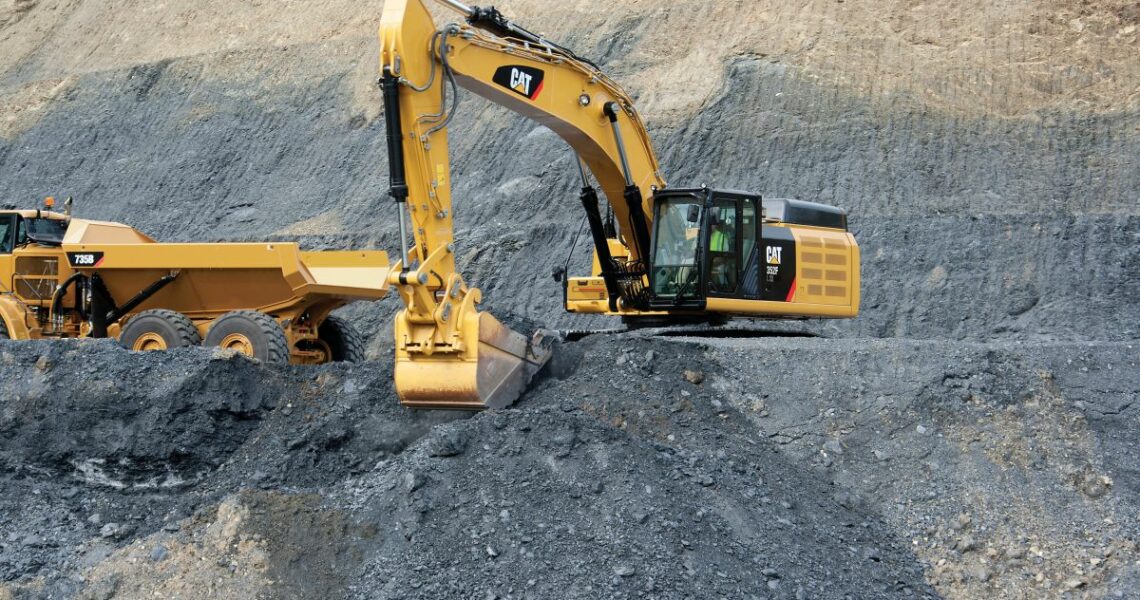
Macht Maschinen munter
Mobile Arbeitsmaschinen wie Bagger, Radlader, Muldenkipper oder Brecher sind nach wie vor – energetisch betrachtet – wenig effizient. Ihr Gesamtwirkungsgrad ist eher bescheiden. Zu viel Energie verpufft bei allen Komponenten nutzlos. Aus diesem Grund setzt sich die Hybridtechnik immer mehr durch, Kraftstoffeinsparungen bis 40 Prozent lassen aufhorchen.
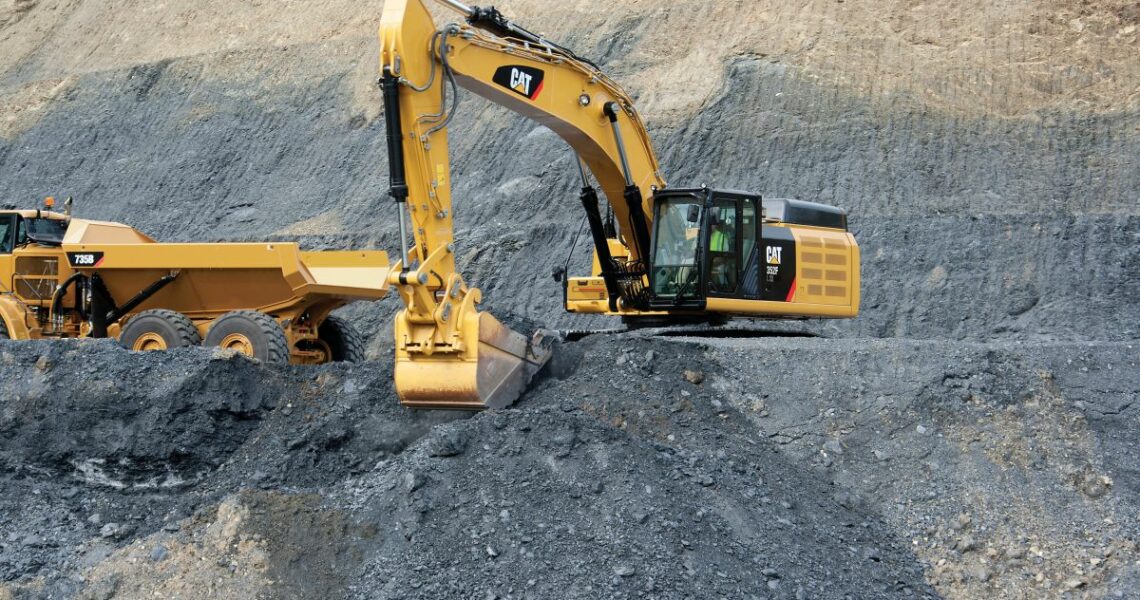
- Drei Antriebs- und Speichervarianten haben sich durchgesetzt
- Volle Leistung bei drastisch weniger Kraftstoffverbrauch
- Weitere Vorteile im Paket inbegriffen
Hybridantriebe bestehen in der Regel aus einem Verbrennungsmotor, einem Energiespeichersystem sowie einem weiteren Antrieb, der die rekuperierte, also die gespeicherte Energie wieder in Form einer mechanischen Dreh- oder Hub-/ Linearbewegung umsetzt. Als Antrieb mobiler Baumaschinen dient meist ein Dieselmotor, der bei Hybridfahrzeugen mit einer weiteren Antriebseinheit kombiniert wird. Durchgesetzt haben sich bisher drei geeignete Antriebs- und damit auch Speicherarten: Erstens die rein elektrische Variante mit Akkumulatoren oder Doppelschicht-Speicherkondensatoren, auch Super-Caps, Power-Caps oder Ultrakondensatoren genannt. Zweitens der Fluidantrieb mit einem Hydraulik- oder Pneumatik-/Gasspeicher sowie drittens die rein mechanische Lösung mit einem Schwungrad als Speichermedium, das meist in einem Hochvakuum läuft. Für all diese Speicherarten gibt es Hybridmaschinen, die bereits in der Praxis eingesetzt werden.
2016 konnten die Projektverantwortlichen des Instituts für fluidtechnische Antriebe und Steuerungen (IFAS) der RWTH Aachen nachweisen, dass mit der Steigerung der Energieeffizienz in der Arbeitshydraulik mobiler Maschinen (Abkürzung: Steam) eine Verbrauchsreduktion von immerhin 40 Prozent möglich ist. Als Basisfahrzeug wählten die Ingenieure in Zusammenarbeit mit Volvo CE den Mobilbagger EW 180C. Anstatt ein herkömmliches Hybridsystem einzubauen, optimierte die Uni-Mannschaft das angeschlossene Hydrauliksystem, um die Verlustmechanismen zu reduzieren. Darüber hinaus wurde eine spezielle Hydraulik-Speicherlösung eingebaut.
Im Gegensatz zu marktüblichen Lösungen wird beim Steam-Bagger weder der Dieselmotor noch die Hydraulikpumpe zur direkten Versorgung der hydraulischen Verbraucher genutzt. Beide werden lediglich zur Aufrechterhaltung des Drucks in jeweils einem von zwei Druckspeichern verwendet. Durch diese sogenannte Speicherladeschaltung lassen sich sowohl der Dieselverbrennungsmotor als auch die hydraulischen Verbraucher unabhängig voneinander steuern; und beide können zur selben Zeit im optimalen Wirkungsgradbereich betrieben werden, da die Konstantdruckleitungen die Energiequelle von den Einflüssen der Lasten trennen. Die beiden installierten Druckspeicher erlauben zudem eine Drehzahlabsenkung sowie eine gleichmäßig hohe Drehmomentbelastung des Dieselmotors, die zu einer deutlichen Verbesserung im Wirkungsgrad führen. Gleichzeitig wird die Rückgewinnung der potenziellen und kinetischen Energie aller Verbraucher ermöglicht. Damit kann die Maschine als ein rein hydraulischer Hybrid bezeichnet werden.
Gegenüber vielen anderen Hybridsystemen, die derzeit entwickelt und verkauft werden, verwendet Steam keine elektrischen Speicher oder Antriebe. Die in der Maschine bereits vorhandene Hydraulik wird lediglich erweitert. So werden viele unnötige Energiewandlungen und Kosten vermieden, wie die Uniforscher extra betonen. Die hydraulische Hybridtechnik erhöht daher die Wirtschaftlichkeit des Baggerbetriebs, dank der drastischen Reduzierung des Kraftstoffverbrauchs um besagte 40 Prozent. Zudem erhalten Betreiber eine höhere Maschinenleistung sowie eine Maschine mit geringerem Geräuschpegel. Die Absenkung der Dieselmotor-Drehzahl von den bisher üblichen 1.800 U/min auf 1.200 U/min führt nämlich zu einer geringeren Geräuschemission und damit zu einer ruhigeren Arbeitsumgebung, die vor allem der Baggerfahrer erfreut feststellen wird.
Spritsparende Hybridtechnik ist verfügbar
Natürlich haben auch viele Hersteller bereits Hybridlösungen im Angebot. Neben Kobelco gilt Komatsu als Vorreiter der kraftstoffsparenden Hybridtechnik. So soll der Kobelco-Raupenbagger SK 210H(N)LC-10 mit seinem Lithium-Ionen-Akkupack rund 14 Prozent weniger Kraftstoff verbrauchen als sein konventionelles Pendant. Bei rund 23 t Betriebsgewicht und 0,7 bis 0,93 m³ Löffelinhalt von hat dieser Hybridbagger eine Leistung von 124 kW (Abgasnorm US Tier 4-final). Zudem konnte seine Produktivität dank Hybridantrieb ebenfalls um 14 Prozent gesteigert werden. Neben der 2.990 mm breiten Standardmaschine gibt es eine schmalspurige Version mit einer Gesamtbreite von 2.800 mm, die sich einfacher transportieren lässt.
Bei seinen beiden leistungsstarken Hybridbaggern HB215-LC2 und HB365-LC3 setzt Komatsu auf Supercaps als Speichermedium für die elektrische Energie. Den HB215-LC2 mit seinen rund 23 t Betriebsgewicht gibt es nunmehr in der dritten Generation. Sein maximales Löffelvolumen beträgt 1,68 m³. Das Hybridsystem besteht aus einem elektrischen Schwenkwerkmotor, einem Generatormotor, einem Hochleistungskondensatorpaket sowie einem 110 kW starken Niederemissionsdieselmotor von Komatsu. Die Supercaps sorgen für die schnelle Speicherung und verzögerungsfreie Bereitstellung der elektrischen Energie. Die kinetische Energie, die beim Abbremsen der Schwenkbewegung in elektrische Energie umgewandelt wird, gelangt über einen Wechselrichter zum Kondensatorpaket, wo sie gespeichert wird. Bei einer höheren Arbeitslast stellt – bevor die Dieselmotordrehzahl gesteigert werden muss – der Hybridcontroller die gespeicherte Energie zur Verfügung, um den Schwenkwerkmotor beim Schwenken des Oberwagens zu unterstützen. Diese durch das Hybridsystem zusätzlich aufgebrachte Energie unterstützt die Leistung des Dieselmotors oder treibt den elektrischen Schwenkwerkmotor an. Anwender berichten, dass sich bei häufigen Schwenkbewegungen, wie sie beispielsweise bei der Beschickung von mobilen Brecheranlagen vorkommen, mit dieser Maschine über 30 Prozent Kraftstoff einsparen lassen. Legt man diese Kraftstoffeinsparung, die aktuellen Dieselpreise sowie die Jahresbetriebsstunden zugrunde, erzielt der Kunde mit solch einem Hybridbagger eine Einsparung zwischen 15.000 und 20.000 Euro pro Jahr. Damit rechnet sich die teurere Hybridtechnik bereits innerhalb von nur zwei Jahren.
Der 36-t-Hybridbagger HB365-LC3 kann mit 255 kW Gesamtsystemleistung und seinem Löffelinhalt von maximal 2,7 m³ große Erdbewegungsarbeiten durchführen. Der emissionsarme 6-Zylinder-Dieselmotor (EU-Stufe IV) leistet 202 kW, dazu kommen dann noch 53 kW elektrische Leistung. In einem Sand- und Kieswerk hat ein Kunde nach längerem Praxiseinsatz erfreut rund 20 Prozent Treibstoffeinsparung festgestellt – im Vergleich zum bereits schon verbrauchsarmen 36-t-Bagger mit reinem Dieselantrieb. Und das sind ermittelte Praxiswerte und keine Prospektangaben. Beide Komatsu- Hybridmodelle sind durch eine spezielle Gewährleistung mit einer Laufzeit von 5 Jahren oder 10.000 Betriebsstunden abgedeckt.
Auf eine andere Technologie setzen Caterpillar und Liebherr, nämlich auf die Hydraulik zur Speicherung der rekuperierten Energie. Beim Cat-Raupenbagger 336F XE etwa speichert ein Hydraulik-Pneumatik-Druckspeicher die Bremsenergie des drehenden Oberwagens und gibt sie bei Bedarf wieder ab. Der Dieselmotor (Cat C9.3 Acert) der 40-t-Maschine leistet 243 kW. Zum Hydraulik-Speicherenergiewert wird keine extra Angabe gemacht, dafür soll die Kraftstoffreduzierung zirka 15 Prozent betragen. Beim Hybridbagger Cat 336F XE sowie beim nächstgrößeren Cat 352F XE (Dieselmotor Cat C13 Acert mit 317 kW) wird die Hydraulik durch ein neues Automatikventil gesteuert. Dieses gewährleistet, dass der Hydraulikstrom jederzeit im erforderlichen Durchflussvolumen und -menge zur Verfügung steht, wie es zur Bereitstellung großer Hub- und Grabkräfte notwendig ist.
Zusatzleistung aus dem Energiespeicher
Der größte Liebherr-Hydroseilbagger HS 8300 HD ist auf Wunsch mit dem selbstentwickelten Hybridantrieb Pactronic lieferbar – ein Hybridantrieb auf Hydraulikbasis. Ein zusätzlicher Energiespeicher, auch Akkumulator genannt, rekuperiert beim Absenken sowie Abbremsen der Last die Energie und gibt diese bei Bedarf (zum Beispiel bei Hub- und Schwenkbewegungen) wieder frei. Beide Bewegungen werden – bei gleichbleibender Primärleistung – dadurch wesentlich erhöht. Daraus folgen mehr Maschineneffizienz und somit höhere Umschlagzahlen. Die Systemleistung entspricht mit 1.250 kW der eines konventionellen Antriebssystems, wobei ein Dieselmotor mit nur 725 kW (Hakenleistung 800 kW) verwendet wird. Mit diesem Pactronic-Hybridsystem lassen sich bis zu 35 Prozent Kraftstoff einsparen, die Umschlagleistung steigt zugleich um denselben Wert. Linear mit dem Kraftstoffverbrauch sinken auch die CO2-Emissionen um bis zu 35 Prozent. Dazu kommen Lärmreduzierung sowie geringere Wartungs- und Servicekosten, man spart sich den Einsatz von aufwendigen Doppelmotoren. Eine Amortisation in nur zweieinhalb Jahren ist allein schon wegen der erheblichen Kraftstoffreduzierung problemlos möglich.
Die Verbindung von Dieselmotor plus Elektro-Motor/-Generator ist schon seit Jahrzehnten in den ganz großen Muldenkippern im Miningbereich üblich. Egal ob Caterpillar 795, Liebherr T282/T284 oder Komatsu 960/980: Alle fahren quasi mit einem Hybridantrieb. Doch erst die Kombination mit einem Rekuperations-/ Energiespeichersystem macht eine vollwertige Hybridantriebslösung.
Mit dem diesel-elektrischen Prallbrecher R3e präsentierte Keestrack kürzlich auf der Intermat die hybride Variante seiner konventionellen Mobilbrecher. Als Antrieb fungiert ein 235 kW starker Volvo-Dieselmotor (Emissionsgrenzwerte gemäß US-Tier 4-final) sowie ein 300-kVA-Generator und ein 132 kW (wahlweise 160 kW) starker Elektromotor. Der schwere 920-mm-Rotor und das Schwerlast-Vibrationsvorsieb arbeiten weiterhin diesel-hydraulisch, während die Versorgung aller Hydraulikkomponenten wie Fahrantrieb, Brechersteuerung, Hubhydraulik, Aufgeber/Nachsieb und Motorkühler ein 45-kW-Elektromotor mit zwei angeschlossenen Load-Sensing-Pumpen übernimmt. Durch die Elektrifizierung lässt sich der Diesel bei verringerter, optimaler Betriebsdrehzahl betreiben, was Kraftstoff spart. Darüber hinaus entfallen diverse Hydromotoren sowie die dazugehörigen Verrohrungen und Schläuche. Zudem sind nur noch 75 l Hydrauliköl an Bord. Das spart Kosten für Service und später die Altöl-Entsorgung. Der Kühlaufwand, Leckage-Risiken sowie die Wartungskosten verringern sich also weiter – besonders vorteilhaft bei mobilen Anwendungen in Stadtgebieten oder Umweltschutzzonen. Noch mehr kann gespart werden, wenn eine nachgeschaltete elektrische Siebanlage (z.B. Keestrack K2e) oder ein Haldenband zusätzlich vom R3e angetrieben wird. Dafür steht ein 63-A-Anschluss zur Verfügung. Das neue optionale Eindeck-Anbausieb bietet mit rund 4,4 m² etwa 30 Prozent mehr Siebfläche als das Vorgängermodell. Die Energiekosten-Einsparungen gegenüber diesel-hydraulischen Antrieben sollen bei dieser vollhybriden Lösung mit optionaler Plug-In-Netzversorgung bei 40 bis 70 Prozent liegen, so verspricht der Hersteller.
Clevere Lösung mit Power-Caps
Das österreichische Unternehmen Rockster macht aus seinem Prallbrecher R1100DE sogar eine Vollhybridvariante, indem es neben der Antriebskombi Diesel- plus Elektromotor die sogenannten Power-Caps einsetzt. Das sind Hochleistungs-Speicherkondensatoren, die elektrische Energie schlagartig speichern und bei Bedarf sofort wieder abgeben können. Da Elektromotoren aus dem Stand innerhalb von Millisekunden ein volles Drehmoment leisten, lässt sich das Brecheraggregat unabhängig vom Lastzustand kontinuierlich und mit gleichbleibender Drehzahl fahren. Der Dieselmotor wiederum arbeitet nahezu konstant bei optimaler Drehzahl, und überschüssige Energie wird eben via Generator in die Power-Caps abgespeichert oder bei Lastspitzen daraus abgerufen – Kraftstoffeinsparung rund 30 Prozent.
Das britische Ingenieurunternehmen Ricardo wiederum entwickelte mit High Effciency Excavator ein Energierückgewinnungssystem für mobile Maschinen, das die Energie mit einem Schwungradspeicher kostengünstig speichert und bei Bedarf wieder abgibt. Auch bei diesem Projekt sind Amortisationszeiten von ein bis maximal zwei Jahren zu erzielen. Eine Kosten-Nutzen-Analyse der verschiedenen Rekuperationslösungen hat gezeigt, dass Hydraulik- sowie die Schwungrad-Energiepeicherung für Bagger besonders interessant sind.
Einbaufertige Lösung aus Köln
Der Kölner Motorenbauer Deutz versteht sich als innovativer Schrittmacher, mit DVERT, der Deutz-Variablen-Emission-Reduktions-Technologie boten die Rheinländer bereits vor Jahren als erste EU-Stufe-V-Dieselmotoren an; verschiedene emissionsarme Gasmotoren gibt es außerdem. Auf der Intermat in Paris stellten die Kölner nun den ersten komplett einbaufertigen Non-Road-Hybridantrieb vor. Statt Dieselmotor und Energiespeicher-/Antriebssystem auf zahlreiche, weit entfernte Einbauorte zu verteilen, die über lange, energiefressende und schaltfaule Leitungen miteinander verbunden sind, präsentiert man quasi eine One-Box-Lösung. Ein 4-Zylinder-Turbo-Diesel vom Typ TCD 2.9 wurde mit einem Elektromotor/-Generator, einer darauf abgestimmten Leistungselektronik sowie einem Lithium-Ionen-Akkupack als Hybridlösung kombiniert. Beides leistet jeweils 55 kW, sodass eine Systemleistung von maximal 110 kW zur Verfügung steht. Das Li-Ion-Akkupack verfügt über eine Kapazität von 40 kWh bei 400 Volt. Die mechanische Anbindung des Elektro-Motor/-Generators an den Dieselmotor erfolgt über ein Getriebe mit integrierter Trennkupplung. Der Diesel lässt sich daher vom elektrischen System komplett abkoppeln, das Fahrzeug kann dann rein elektrisch betrieben werden. Vorteil der Hybridtechnik ist, dass ein kleinerer Verbrennungsmotor gewählt werden kann, der zudem immer im optimalen Drehzahlbereich arbeitet – mit Kraftstoffeinsparungen bis 30 Prozent und mehr. Zudem lassen sich verbrauchssenkende Zusatzfunktionen wie Start-Stopp oder Kurbelwellenstart einsetzen sowie Nebenantriebe rein elektrisch betreiben. Auch als Stand-alone-Lösung zum Antrieb von stationären Maschinen oder Förderbändern eignet sich dieses Hybridantriebspaket.