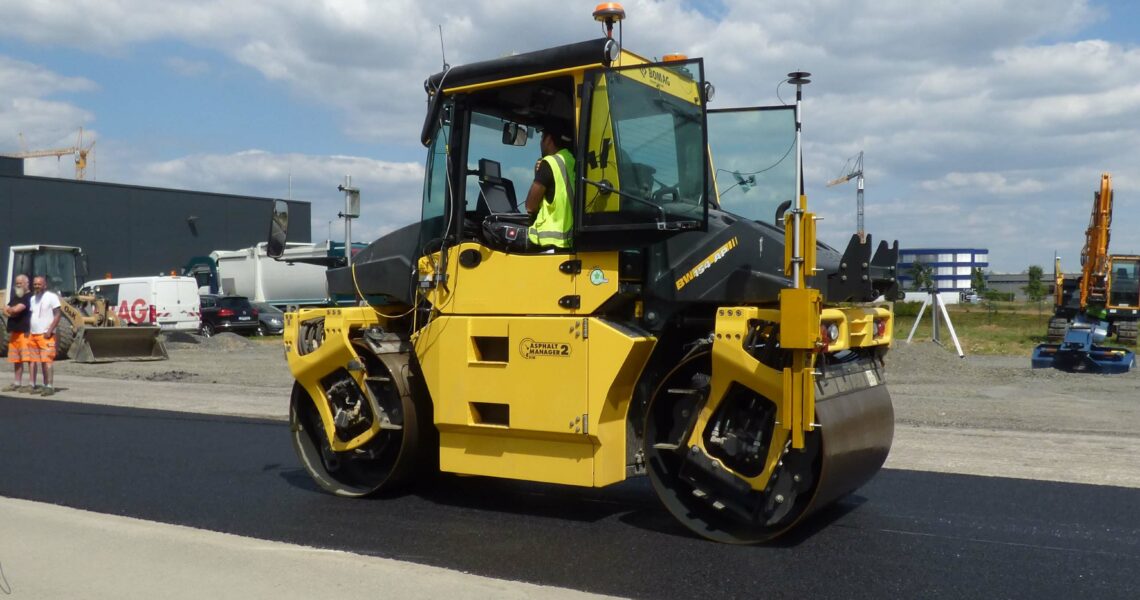
QUASt: Forschungsprojekt beim Asphalteinbau
Um wesentliche Qualitätsparameter beim Asphalteinbau nicht erst hinterher, sondern schon während des Einbauprozesses messen und gegebenenfalls sofort korrigieren zu können, wurden mit dem Forschungsprojekt QUASt neue Lösungsansätze zur Prozessüberwachung erarbeitet. Unlängst wurden nun am Moba-Firmensitz in Limburg an der Lahn die Ergebnisse präsentiert.
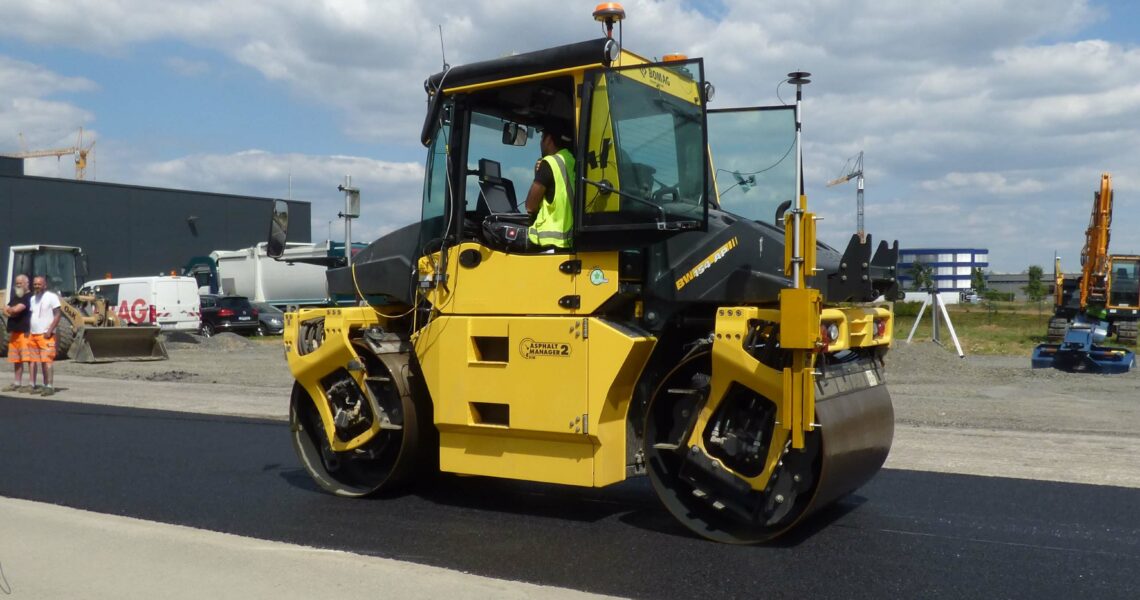
Herkömmlicherweise werden beim Asphalteinbau Abweichungen vom Soll erst nach abgeschlossenem Einbauprozess festgestellt: dann nämlich, wenn das Endergebnis überprüft wird. Ein Eingreifen ist dann jedoch nicht mehr möglich, gegebenenfalls entstandene Fehler müssen ausgebessert, also ausgefräst und neu asphaltiert werden. Mit dem Forschungsprojekt QUASt – neue Ansätze bei der Qualitätsüberwachung im Straßenbau – haben die Forschungspartner Androtec, Bomag, Moba Mobile Automation, TH Köln, TPA (Strabag) und RWTH Aachen Lösungsansätze erarbeitet, um früher reagieren zu können. Gefördert wurde das Projekt durch die Bundesanstalt für Straßenwesen (bast).
Die gute Nachricht: Das Forschungsziel wurde erreicht. Die maßgeblichen Parameter – Breite, Dicke und Querprofil des Belags, Längsebenheit und Verdichtungsgrad – lassen sich flächendeckend nun schon während des Einbauprozesses überwachen. Neu am Ablauf ist unter anderem, dass die Walze nun nicht mehr rein als abschließendes Verdichtungswerkzeug fungiert, sondern als Messinstrument das Einbau-Ergebnis vermisst und die Messwerte mit den vorgegebenen Referenzwerten abgleicht. Dabei werden alle Stationen des Einbauprozesses – von der Mischanlage und dem transportierenden Lkw über Beschicker und Fertiger bis zu Splittstreuer und Walze – in einen Regelkreis integriert und bei notwendigen Korrekturen direkt in Echtzeit angesprochen.
Anders als beim Projektvorläufer PASt (prozesssicherer automatisierter Straßenbau), bei dem die Automatisierung des Straßenfertigers im Zentrum stand, lag der Fokus bei QUASt nun auf der kompletten Fertigungskette. Und auch künftig werde, so der stellvertretende bast-Referatsleiter Oliver Ripke, dem Fortschritt in der Digitalisierung Rechnung getragen. Ein wichtiger Aspekt sei dabei, mit der Autonomisierung von Baumaschinen die Sicherheit des Straßenbaupersonals zu vergrößern – insbesondere des besonders gefährdeten Mitarbeiters an der Fertigerbohle auf Baustellen im rollenden Verkehr, dessen ständige Präsenz direkt an der Bohle nicht mehr erforderlich sein werde. Der Startschuss für das Folgeprojekt Robot – Straßenbau 4.0 ist bereits gefallen.
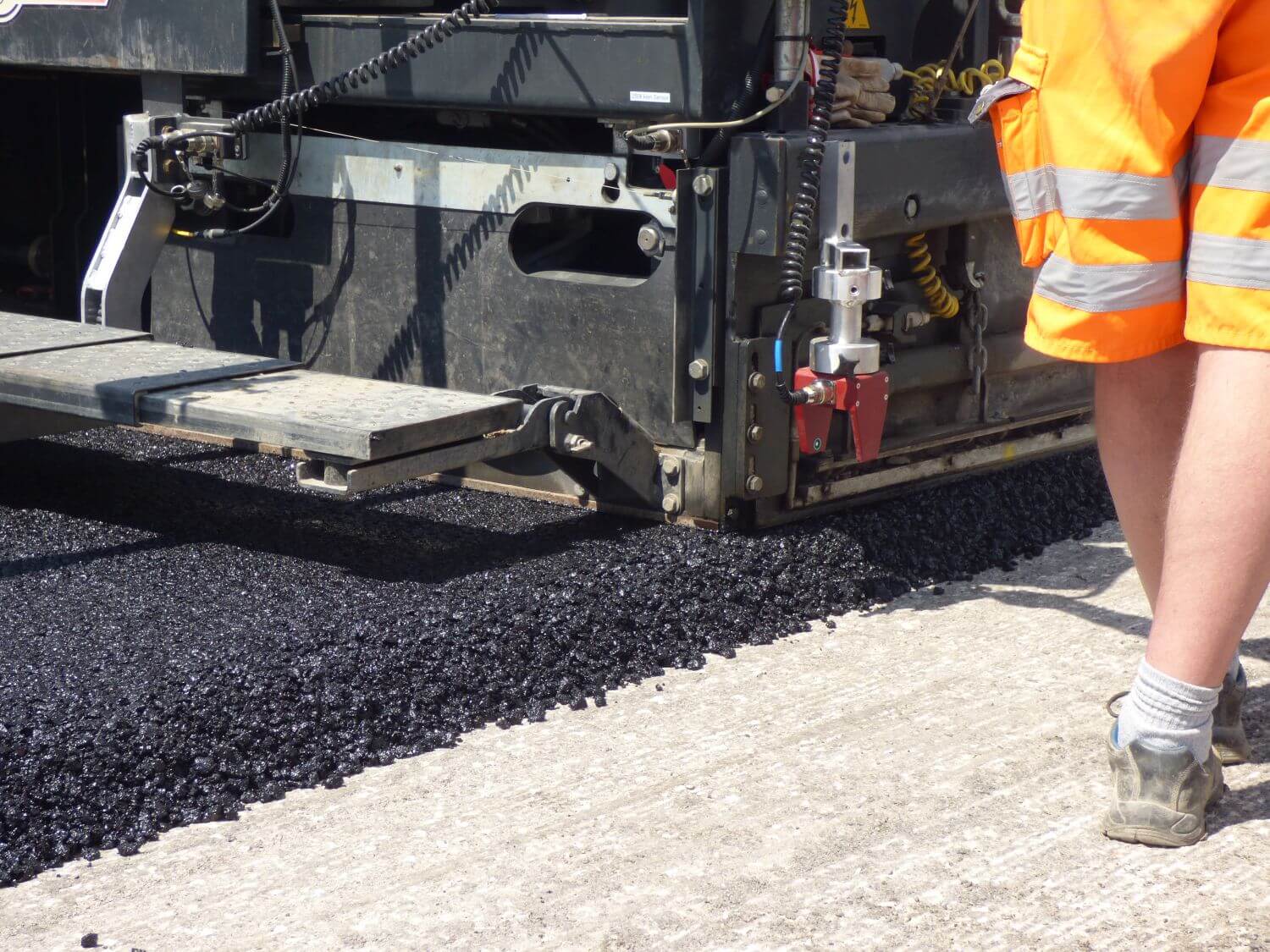
Die schwimmende Bohle am Fertiger ist laut Prof. Alfred Ulrich von der TH Köln, Leiter des QUASt-Projekts und Gründer des ebenfalls beteiligten Kölner Labors für Baumaschinen (KLB), eine besondere Schwierigkeit bei der Erfassung von belastbaren Messdaten. Die Erfassung der extrem komplexen Aspekte ihrer Arbeit war daher eine besondere Herausforderung bei dem Projekt.
Die Vergrößerung der Transparenz durch Echtzeit-Messwerte ist wiederum eine Kernkompetenz der Moba Mobile Automation. Deren Entwicklungsvorstand Alfons Horn erläuterte die umfangreichen Messkonzepte für Fertiger und Walze. Ziel sei immer ein „stabiles, störungsfreies und robustes Arbeiten“, Unterbrechungen könne man sich in der Praxis nicht erlauben. Produkte, die die Ebenheit steuern (Mobamatic II und Big-Sonic-Ski) oder Schichtdicke (Pave-TM) bzw. Temperatur des Einbaumaterials (Pave-IR) messen und dokumentieren sowie die flächendeckende Verdichtungskontrolle (MCA-3000) hätten sich am Markt bereits bewährt und wurden, wie das Schichtdicken-Messsystem Pave-TM, preisgekrönt (VDBUM-Förderpreis, Bauma-Innovationspreis). Und sie konnten im Rahmen von QUASt weiterentwickelt und nochmals verbessert werden.
Die Verdichtung ist eine zentraler Qualitätsfaktor
Ein ebenso wichtiger Aspekt bei der Optimierung der Einbauqualität ist die Berechnung der erreichten Verdichtung. Sie lässt sich nämlich nicht direkt messen, wie beispielsweise Länge oder Breite, sondern wird mithilfe diverser Parameter errechnet. Für den Fertiger gilt: Aus dem eingebauten Volumen (Wegstrecke x Bohlenbreite x Einbaustärke) und der dafür aufgewendeten Masse (angelieferte Tonnagen abzüglich der verbleibenden Restmenge) ergibt sich die Dichte der eingebauten Schicht und damit die Vorverdichtung. Für die Walze kommt noch das Setzmaß hinzu: Mit einem Laser als Höhenreferenz wird die erreichte Reduzierung der Schichtdicke für jede Walzenüberfahrt ermittelt und damit das veränderte Volumen – und die neue Verdichtung der eingebauten Schicht.
Natürlich müssen alle Berechnungswerte so exakt wie möglich ermittelt werden, daher wurden die Möglichkeiten zur Messung der einzelnen Parameter weiter verbessert. Für die Wegstrecke wird die Arbeitsgeschwindigkeit des Fertigers mit hochgenauen GNSS-Messungen und Bewegungs-Triggern ermittelt. Die Schichtdickenmessung wurde weiter optimiert. Herausforderung war und bleibt die Ermittlung der Menge des bereits eingebauten Materials – denn was der Fertiger von der geladenen Menge tatsächlich bereits eingebaut hat, lässt sich nicht so einfach messen. Doch mit fortschreitender Einbauzeit und steigender Anzahl verbauter Lkw-Ladungen addieren sich die Abweichungen nicht auf, sondern werden verschwindend klein.
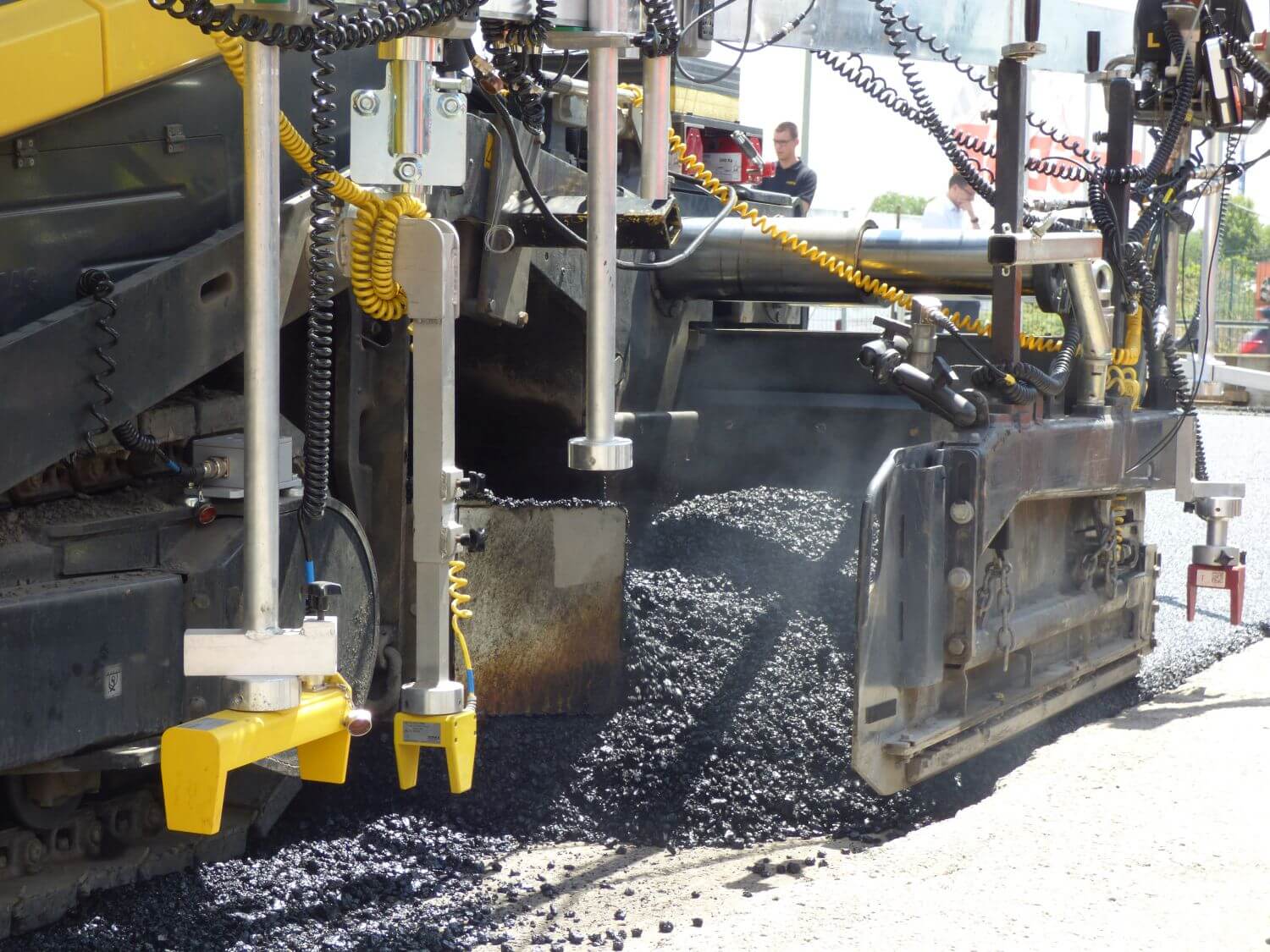
Eine neue Dimension bei der Laservermessung stellte Androtec-Geschäftsführer Michael Kasper vor: Mit Dynaplane erfolge die Referenz nicht mehr – wie aktuell Standard – über eine Messebene, die durch einen rotierenden Laserstrahl aufgespannt wird. Das neue System arbeite mit einem Messraum in Form zweier Kegel, die sich an der Spitze (am Ausgangspunkt des Lasers) berühren. Sie entstehen durch eine taumelnde, schräg stehende Laserebene, die erforderlichen Sensoren können viel kleiner und punktförmig sein. Höhen- und optional Positionsbestimmungen seien jetzt in einem Umkreis von 400 m und bis 80 m Höhe möglich. Dieses System messe so präzise, dass sogar temperaturbedingte Ausdehnungen von Stativen und Masten berücksichtigt werden.
Dank der TPA – Gesellschaft zur Optimierung von Technischen Prozessen, Arbeitssicherheit und Qualität aus Strabag-Konzernverbund – konnten alle Testergebnisse in der Praxis erprobt und auf dem Moba-Testgelände live präsentiert werden. Mit einem Fertiger und einer Walze von Bomag wurde eine Demonstrationsstraße eingebaut. Die gezeigten sogenannten Demonstratoren werden nun zu Prototypen weiterentwickelt, um nach erlangter Serienreife den Straßenbau zu optimieren. Die Forschungspartner erwarten, dass der Einbauprozess für das Straßenbaupersonal sicherer wird und dass Zeit, Geld und wertvolle Ressourcen eingespart werden können – weil es möglich ist, entstehende Abweichung direkt zu erkennen und zu beheben.