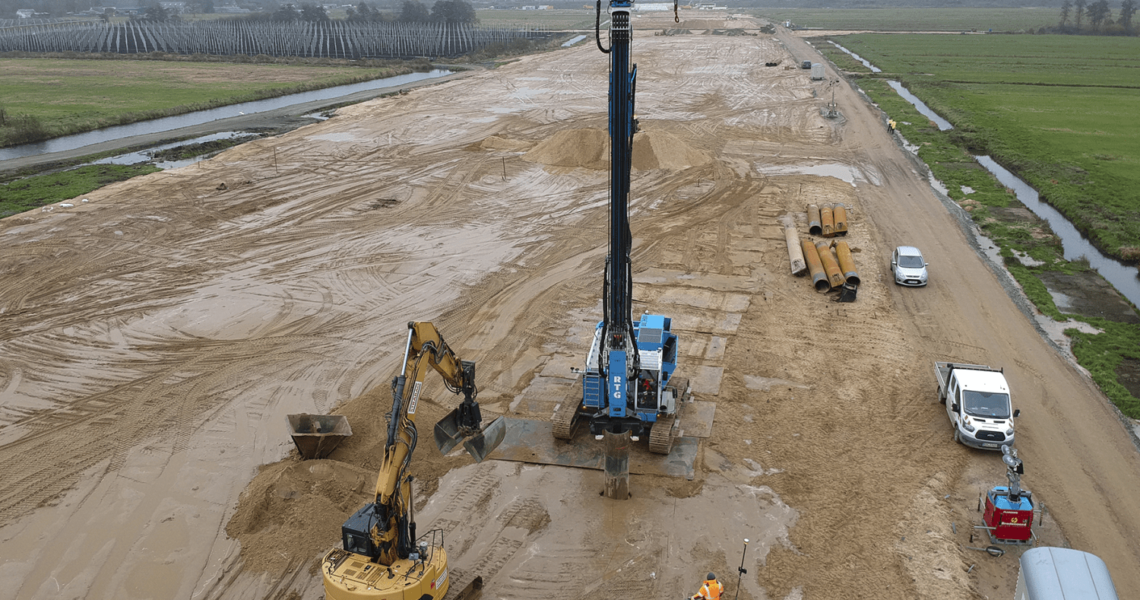
GEC-Säulen bis ganz nach unten
Der rund 8 km lange Bauabschnitt der A26 zwischen der Landesgrenze Niedersachsen und der A7 in Hamburg erfordert aufwendige Vorarbeiten. Schwierige geologische und hydrogeologische Bodenverhältnisse – teilweise wassergesättigter Torfboden – sorgen dafür, dass der Baugrund erst konsolidiert und stabilisiert werden muss. Dafür sind sogenannte Geotextile Encased Colums (GEC) in Kombination mit Vertikaldrains und einer Auflastschüttung vorgesehen.
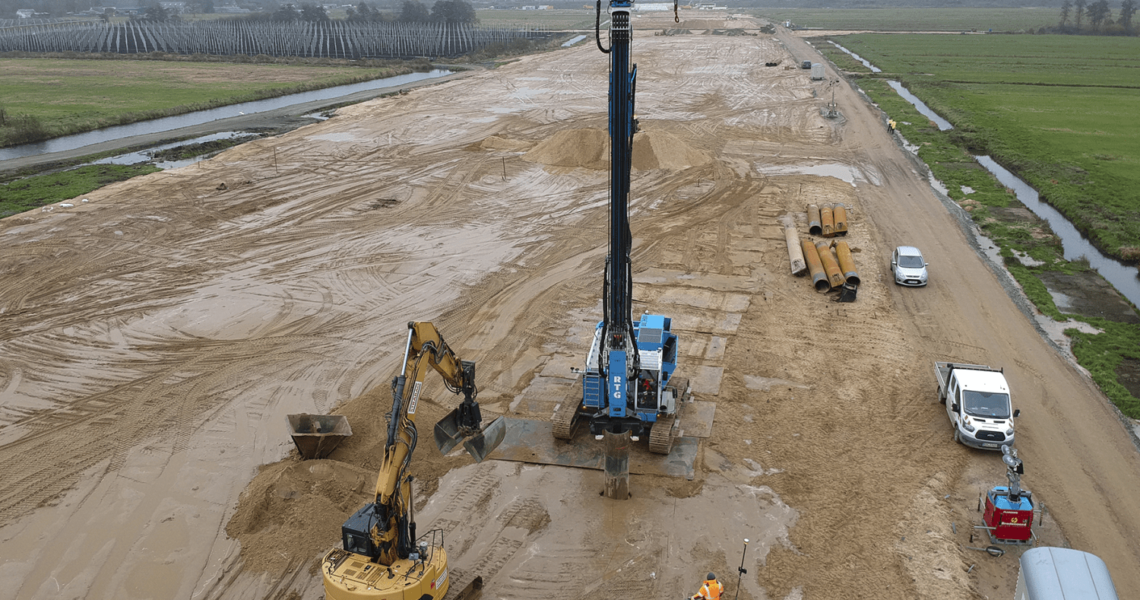
Insgesamt werden rund 55.000 GEC-Säulen hergestellt, die die Lasten in die tragfähigen Bodenschichten ab- und gleichzeitig durch ihre Drainagewirkung zur Konsolidierung des Baugrunds beitragen. Dabei kommen auch zwei RTG-Mäkler von Thyssenkrupp Infrastructure zum Einsatz.
Bereits seit 2002 wird die neue Bundesautobahn 26 als Verbindung zwischen der künftigen A20 (Autobahnkreuz Kehdingen) in Niedersachsen bis nach Hamburg-Stillhorn (A1) gebaut. Die gut 59 km lange vierspurige Autobahn soll bis 2031 komplett fertig sein. Dabei hat die Trasse der A 26 eine besondere Lage zwischen dem Natur- und Vogelschutzgebiet Moorgürtel und dem Obstanbaugebiet Altes Land. Aufgrund der bundesländerübergreifenden Streckenführung gibt es unterschiedliche Bauherren. Verantwortlich für die Trassenabschnitte auf Hamburger Gebiet und damit den aktuellen Bauabschnitt ist die Deges (Deutsche Einheit Fernstraßenplanungs- und -bau), die Bauausführung erfolgt durch die Arge A26-A7-Strabag-Bunte. „Wir haben es hier mit einem sehr schlechten Baugrund zu tun“, erläutert Hans Peter Beye, Bauleiter der Strabag, Direktion Großprojekte Nord-West. Erst in ungefähr 9 m Tiefe beginnen feste Sandschichten, die die Lasten der neuen A26 abtragen können. Darüber liegt eine weiche Torfschicht. Daher werden für die Lastableitung Tragelemente benötigt, die bis in die Sandschichten reichen.
Nach Abwägung aller alternativen Gründungsvarianten hat sich der Bauherr für das GEC-System entschieden. Vorteil gegenüber anderen Säulensystemen: Die Sandsäulen sind durch die nahtlos ringgewebte, hoch reißfeste Geotextil-Ummantelung flexibel und können ein Stück weit auch die Schwingungen aus der späteren Belastung durch den Verkehr mitmachen. Bei Säulen aus Beton besteht beispielsweise die Gefahr, dass sie auf Dauer durch die Schwingungen brechen und rechnerisch nach 50 bis 60 Jahren ausgetauscht werden müssten. Außerdem haben die GEC-Säulen eine entwässernde Wirkung. So werden auf der gesamten Breite des Bauabschnitts von 55 m etwa 55.000 Geotextile Encased Colums teilweise bis zu 11 m tief bis in die Sandschicht errichtet. Das entspricht ungefähr 20 Prozent der Gesamtfläche, bei den restlichen 80 Prozent kommen Vertikaldrains zum Einsatz.
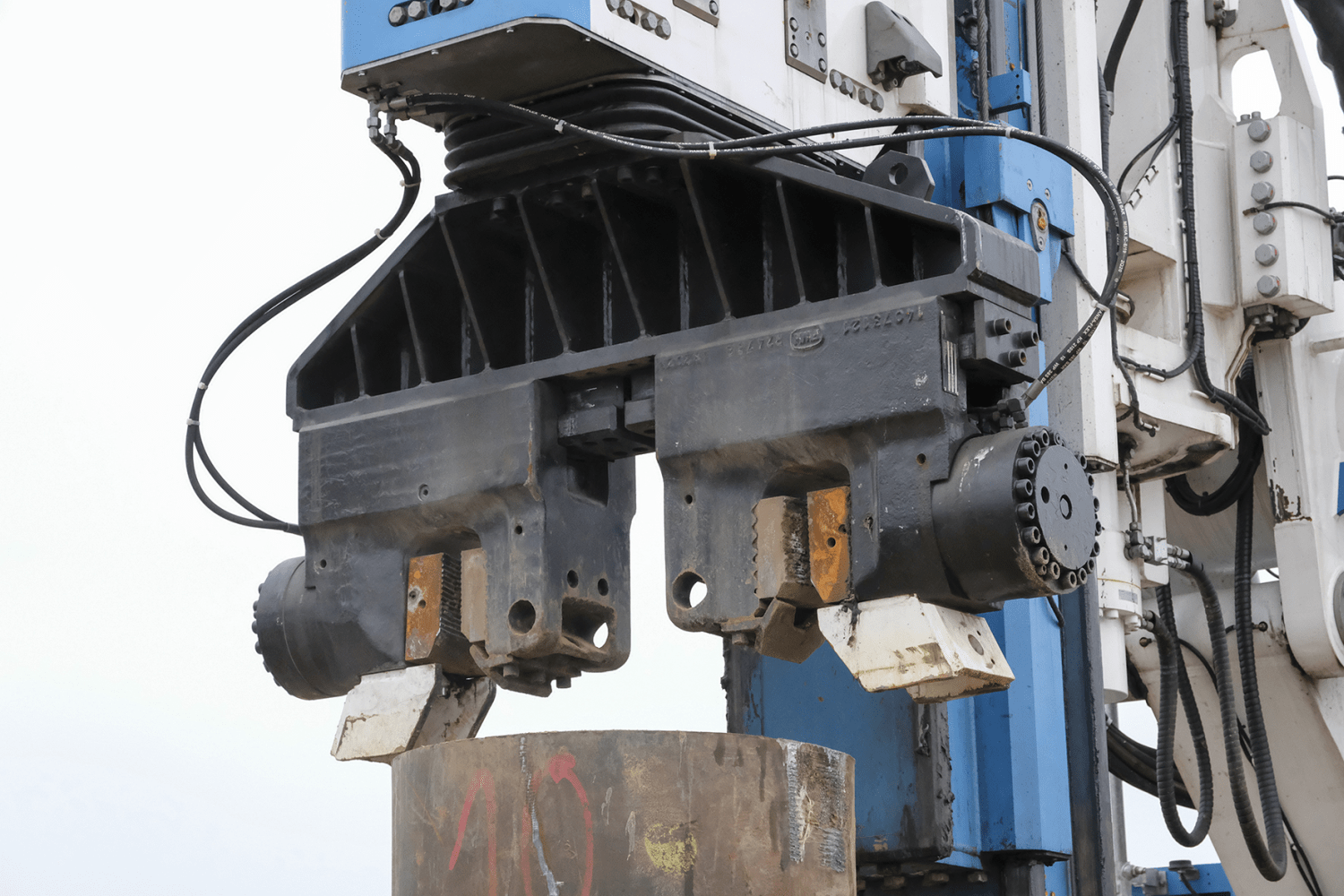
Hergestellt werden die GEC mithilfe des Verdrängungsverfahrens. Dabei vibrieren aktuell zwei leistungsstarke RTG-Mäkler – RG 16T und RG 21T – von Thyssenkrupp Infrastructure Stahlrohre in die Tiefe. Diese haben am unteren Ende eine geschlossene, spitz zulaufende Doppelfußklappe, die den weichen Torfbaugrund verdrängt. Es entsteht eine Röhre, in die zunächst das vorkonfektionierte Geotextil eingebracht wird. Anschließend erfolgt die Sandfüllung. Ist das Geotextil innerhalb des Stahlrohrs komplett mit Sand gefüllt, wird das Stahlrohr mit dem RTG-Mäkler vibrierend aus dem Boden gezogen. Dabei öffnet sich die Doppelfußklappe und der Sand wird durch die Vibrationen und sein Eigengewicht zu einer kompakten Säule verdichtet.
„Den unteren Bereich der Säule befüllen wir zunächst mit einem Sand-Bentonit-Gemisch, sodass eine zirka 2 m starke Dichtungsschicht entsteht“, erklärt Beye. Die soll verhindern, dass das gespannte Grundwasser unterhalb der Torfschicht an die Oberfläche gelangen kann. „Es soll nur der Torf entwässert werden“, so Beye. Denn neben der lastabtragenden Funktion übernehmen die Sandsäulen auch die Drainage bei der Konsolidierung des Baugrunds. Das geschieht durch das sogenannte Auflastverfahren. Dabei wird der Bereich der späteren Autobahntrasse mit aufgeschüttetem Sand belastet. Durch sein Eigengewicht wird das Porenwasser aus dem Torf gedrückt und gelangt durch die Sandsäulen bzw. die Vertikaldrains an die Oberfläche. Auf diese Weise nimmt man die Setzungen des Baugrunds vorweg und macht ihn tragfähiger, um Schäden an der späteren Fahrbahn zu vermeiden.
Sind auf einer größeren Fläche mehrere Säulen hergestellt, wird ein weiteres Geotextilgewebe bahnenweise wie ein Teppich auf der Fläche ausgelegt und mit Sand zur Belastung überschüttet. Dabei ist die Aufschüttung 3 m höher als die spätere Gradiente der Autobahn und bleibt rund vier Monate bestehen, bis der Boden auskonsolidiert und der Setzungsvorgang abgeschlossen ist. Anschließend wird der Sand abgetragen und das Material an anderer Stelle wiederverwendet. Die Sandauflast führt auch zur Aktivierung der Ringzugkräfte in der Geotextilummantelung. Im Schnitt haben die 800 mm durchmessenden Säulen untereinander 2 m Abstand und sind in einem vorher berechneten Wabenraster angeordnet.
Das Einrütteln von Rammgut ist die Hauptanwendung der RTG-Mäkler. Dabei sind die Teleskopmäkler von RTG zur Übertragung hoher Zug- und auch Druckkräfte sowie zur Aufnahme von Drehmomenten ausgelegt. „Mit dem leistungsstarken Hydraulikrüttler MR 150 AVM lassen sich die Stahlrohre zur Herstellung der GEC gut in den Baugrund ein- und auch wieder ausrütteln. Die hohe Motorleistung von 563 kW des Trägergeräts sorgt für ausreichend Leistungsreserven, falls es der Boden“, so Robert Haupt, Leiter des Regionalbereichs Nord bei Thyssenkrupp Infrastructure. Eine weitere Besonderheit: „Die Getriebeschmierung erfolgt bei dem Rüttler durch das Hydrauliköl der Trägergeräte. So haben die Geräte eine verbesserte Öltemperaturbegrenzung im Dauerbetrieb.“ Zusätzlich verfügen die Mäkler über das patentierte Silent-Vibro-Paket: Es umfasst neben der Schalldämmung des Federjochs und der Integration der Hydraulikinstallation in das Federjoch auch die komplette Einkapselung des Frontbereichs einschließlich der Hydraulikmotoren sowie eine Schallisolierung zwischen Federjoch und Klemmzange über ein flexibles Formelement.
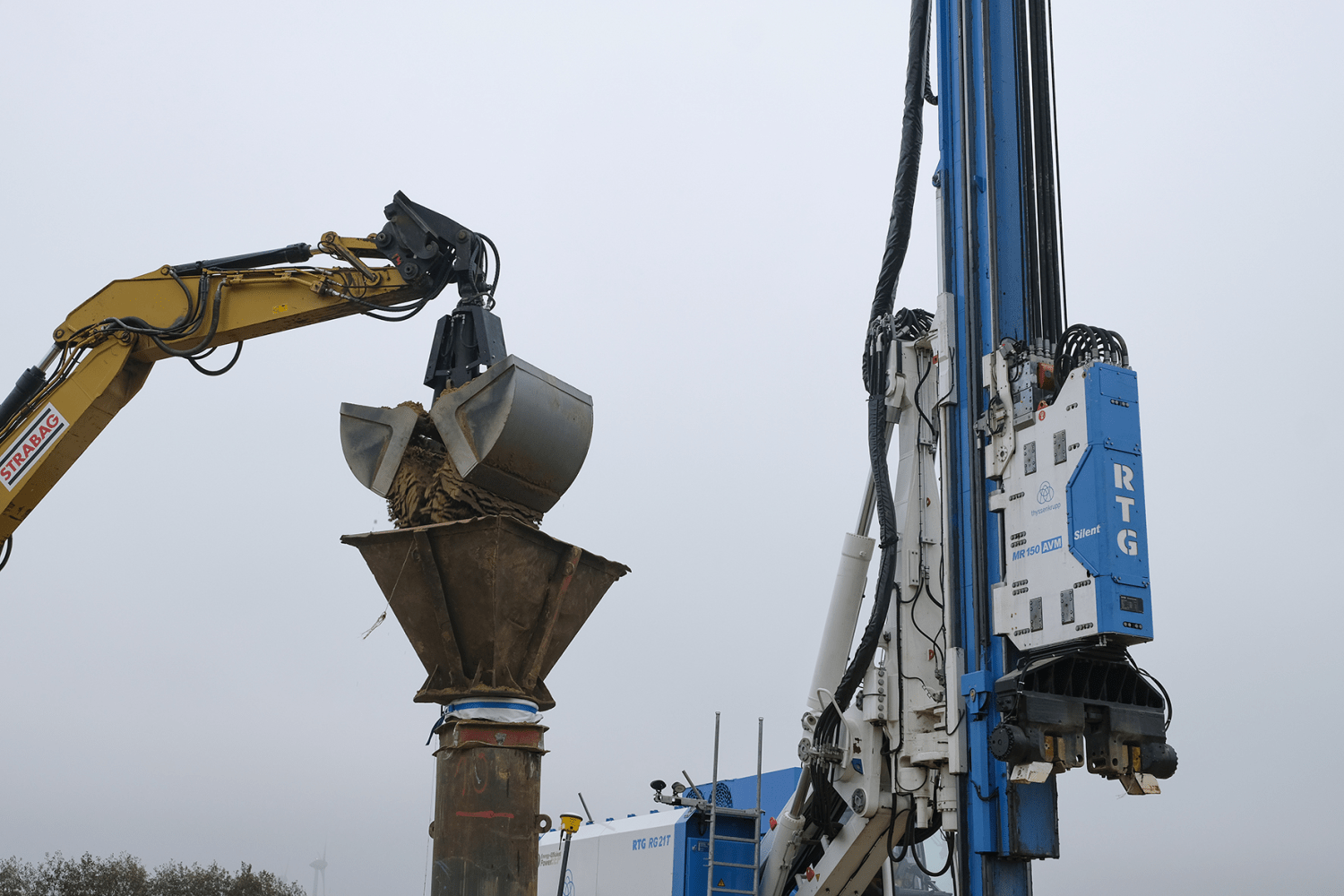
Sämtliche Anbaugeräte der Mäkler sind innerhalb einer Baureihe austauschbar – mit dem automatischen Schnellkupplungssystem ACS sogar in wenigen Minuten. Dazu kommen kompakte Transportabmessungen, kurze Rüstzeiten sowie die geringe Lärmbelastung für die Geräteführer. Ende 2023 will die Strabag die Arbeiten auf diesem Bauabschnitt beendet haben. Dann ist der Vorbelastungsdamm erstellt und der Boden tragfähig, sodass der eigentliche Bau der Fahrbahn beginnen kann.
Auch künftig ist Thyssenkrupp Infrastructure für Projekte dieser Art gerüstet, erst im April 2021 verlängerte sich der seit 2018 bestehende Partnerschaftsvertrag mit der RTG Rammtechnik. So bleibt Thyssenkrupp Infrastructure auch weiterhin exklusiver Händler für RTG-Produkte in Deutschland, Österreich und Dänemark. RTG ist seit über 20 Jahren innerhalb der Bauer-Maschinen-Gruppe der Spezialist für Vibrations-, Ramm- und Presstechnik.