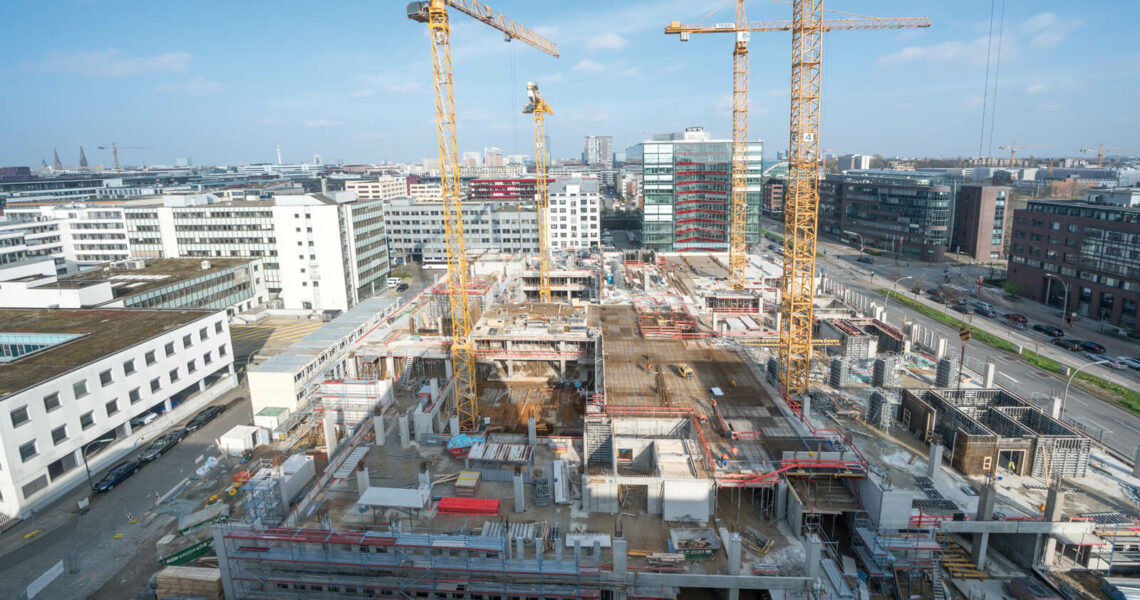
Hünnebeck-Schalkonzept optimiert Vorhaltemengen
Vom Untergeschoss bis in die elfte Etage mit demselben Schalmaterial arbeiten. So lautete bei der Hamburger Großbaustelle Olympus-Campus die Vorgabe der Bauleitung an den Schallieferanten – denn Lagerflächen gibt es praktisch keine. Überzeugt hat ein ungewöhnliches Konzept von Hünnebeck mit optimierten Vorhaltemengen. Mehrere Decken- und Wandschalungen des Herstellers sind beim eng getakteten Innenstadtprojekt im Dauereinsatz.
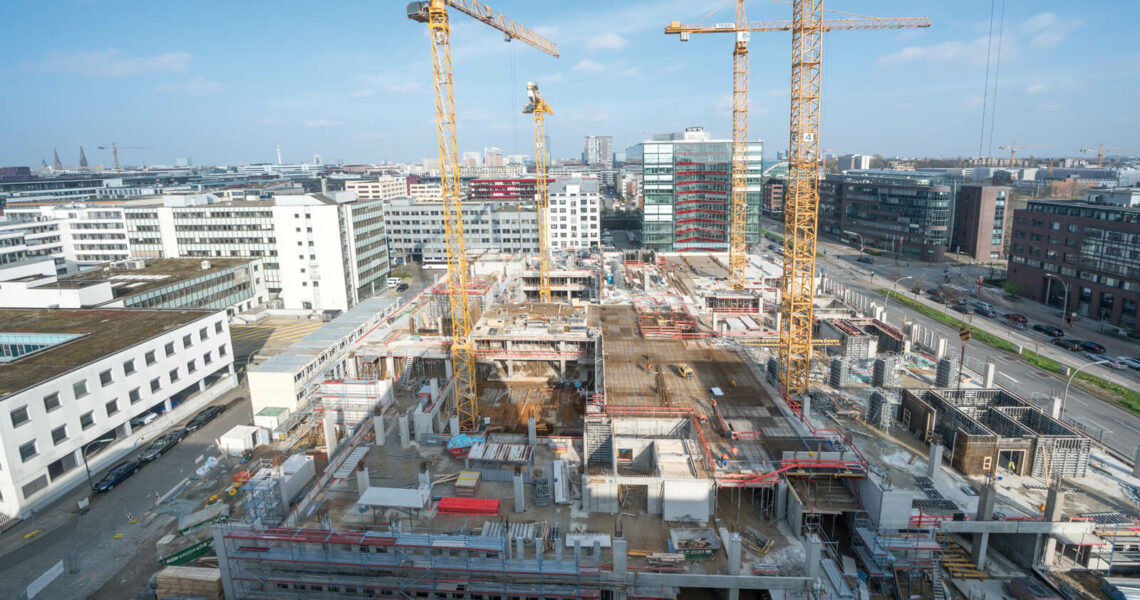
Der japanische Olympus-Konzern erweitert seinen Standort Hamburg und baut dazu im Stadtteil Hammerbrook eine moderne Unternehmenszentrale. 55.000 oberirdische und fast 24.000 unterirdische Quadratmeter Fläche sollen den Mitarbeitern nach der Fertigstellung 2020 eine attraktive Arbeitsumgebung bieten – mit Rückzugsarealen, Cafés und Sporteinrichtungen. Das Konzept des Hamburger Architekturbüros gmp sieht dafür drei Baukörper vor: An einen elfgeschossigen Hauptbau mit Foyer und überdachtem Atrium schließen sich, leicht versetzt, zwei L-förmige Gebäude an. Olympus realisiert das Projekt mit der Zech-Gruppe im Rahmen eines Joint-Ventures. Sämtliche Planungs- und Bauleistungen wurden von der Projektgesellschaft im Rahmen eines Generalübernehmer-Modells an die Arge Olympus-Campus übertragen, die sich aus der Hamburger Niederlassung von Zech Bau und Rom Technik aus Stuttgart zusammensetzt.
Beim Rohbau arbeitet Zech Bau eng mit den Schalungsexperten von Hünnebeck zusammen. „Wir haben gemeinsam ein Schalkonzept entwickelt, das es ermöglicht, vom Untergeschoss bis in die oberste Etage mit demselben Schalmaterial zu arbeiten“, so das baubetreuende Hünnebeck-Team. So kann die Vorhaltemenge auf der Innenstadt-Baustelle, die praktisch keine Lagermöglichkeiten bietet, so niedrig wie möglich gehalten werden. Sämtliches vorhandene Schalmaterial ist nahezu permanent im Einsatz. Das sind rund 4.000 m2 Deckenschalung, bestehend aus Stahlrahmen-Deckenschaltischen der Topmax-Serie und Topec-Modulschalung. Dazu kommen etwa 1.600 m2 Manto-Großrahmenschalung und zehn einsatzfertige Säulenschalungen.
Dabei erwies sich eine ungewöhnliche Idee der Schalprofis als effizient: Bereits ab den Untergeschossen arbeitet das Hünnebeck-Team mit den Topmax-Deckenschaltischen. „Wir haben den Einsatz der Tische natürlich detailliert geplant, um sie auch aus den unterirdischen Bereichen leicht herausholen zu können“, erklären die Schalungsplaner. „Jetzt, in den bis zu elf Etagen hohen Obergeschossen mit ihren offenen Fassaden, können die Tische prima als absturzsichere auskragende Schalung eingesetzt werden.“ Dank ihrer umlaufend kantengeschützten Schalhaut aus Ecoply-Vollkunststoff und den robusten, 12 cm hohen, pulverbeschichteten Stahlrahmen ergibt sich für die Topmax-Tische ein minimaler Reinigungsaufwand während ihres nahezu ununterbrochenen Einsatzes. Durch die Kompatibilität zum Protecto-Seitenschutzsystem sind die in der Schalung stehenden, auskragenden Deckenränder zudem absturzgesichert. Ein weiterer Pluspunkt des Topmax-Systems: Mittels Kanthölzern, die mit einem speziellen Halter in die Tische eingehängt werden, lassen sich laut Hersteller auch Pass- und Ausgleichsflächen einfach schalen.
Die Topmax-Tische werden auf der Hamburger Baustelle in Kombination mit der von Hand zu bedienenden Topec-Modulschalung eingesetzt – Topmax und Topec im Verhältnis 70:30. „Mit dieser Mischung lassen sich alle Geschosse von unten bis oben gleichermaßen schalen“, so die Planer. Die Topec-Schalung verwendet das Team an den kleinteiligeren inneren Deckenbereichen, denn die 1,8 x 1,8 m großen Tafeln lassen sich vom Boden aus mit wenigen Handgriffen von zwei Bedienern montieren: Tafel einhängen, hochschwenken, abstützen. Eine schalungstechnische Herausforderung war die gut 7,5 m hohe und etwa 800 m2 große Foyerdecke im Eingangsbereich des Hauptgebäudes. Hier mussten die Topmax-Tische mit einem Gass-Schalungsgerüst unterstützt werden. Das Alu-Baukastensystem besteht aus lediglich drei Basiskomponenten: Stütze, Mittelstück und Rahmen. Da das schwerste Teil nur 22 kg wiegt, die Tragfähigkeit pro Stiel aber bis zu 140 kN beträgt, lassen sich den Angaben nach aus wenigen Gass-Elementen schnell leistungsfähige Konstruktionen montieren.
Als Wandschalung setzte man auf der Olympus-Baustelle die Manto-Großrahmenschalung ein. Verwendet wurden davon hauptsächlich die 240 x 330 cm messenden Großtafeln, die mit einer speziellen Richtzwinge fest und fluchtend verbunden werden. Mit 14 cm Rahmenstärke und innenliegenden Versteifungsrippen ist die Wandschalung bis 3,3 m Höhe für einen Betondruck von 80 kN/m2 ausgelegt. Mit dem effizienten Schalkonzept für Wand und Decke ist auch die Bauleitung zufrieden: „Durch die geschickte Wahl der eingesetzten Schalungen haben wir nach oben hin tatsächlich keine Systemwechsel und daher auch keine ungenutzten Vorhaltemengen. Wir stellen alle Geschosse mit demselben vorhandenen Material her. Als wir uns vor Baubeginn nach dem passenden Schalungslieferanten umgesehen haben, war das unsere Hauptbedingung.“