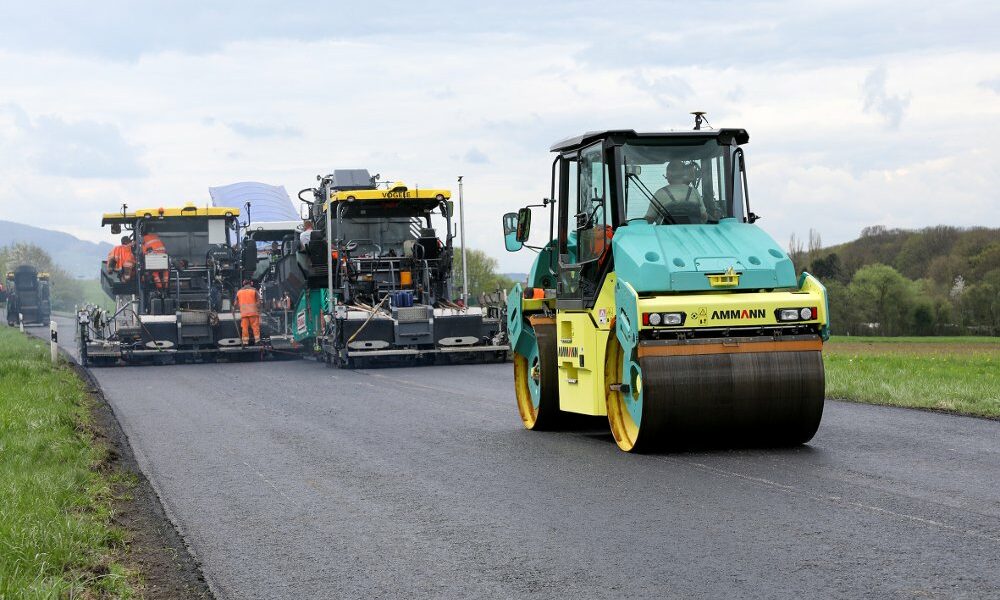
Die ganze Kette immer transparent
Zwei Jahre lang wurde bei Bad Boll nahe Stuttgart die Qualitäts-Baustelle der Zukunft erprobt. In vier Bauabschnitten auf zwei Teststrecken wurde viel darüber gelernt, wie man den Bauprozess stabiler und die Qualität der eingebauten Straßen verbessern kann. Diese Erkenntnisse sind jetzt der Ausgangspunkt für eine neue Praxis, die bereits bei Ausschreibungen gefordert werden soll.
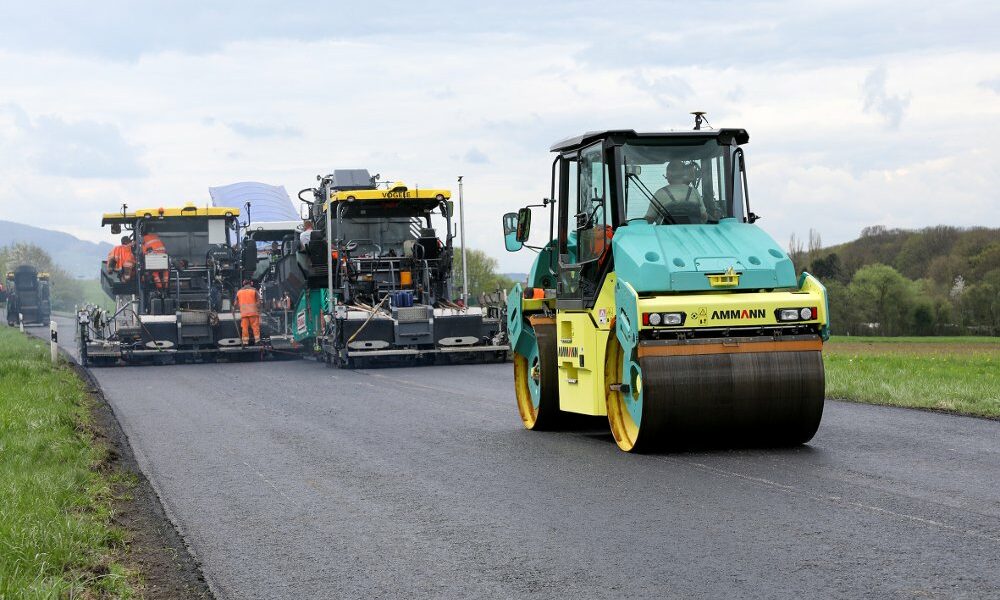
Jetzt hängt es von den Straßenbauverwaltungen ab, inwieweit die Erkenntnisse des Pilotprojekts Qualitätsstraßenbau 4.0 konkret umgesetzt werden. Zwei Jahre hat ein Expertenteam aus vier Unternehmen unter der Leitung der Industrie-4.0-Experten von Drees & Sommer getestet, wie die unsteten Prozesse im Straßenbau verlässlicher und die gebauten Straßen damit hochwertiger und langlebiger werden können. Neben Systemlösungsanbieter Topcon engagierten sich dabei Baumaschinenhersteller Ammann, Softwarehersteller Ceapoint und das Bauunternehmen Strabag. Den Einbau der ersten Tragschicht des letzten Teilstücks konnten Vertreter von Straßenbauverwaltungen vor Ort mitverfolgen. Jetzt könnten sie die Erkenntnisse in die Ausschreibungspraxis und damit auf die Baustellen bringen.
Dr. Burkhard Seizer, Infrastrukturberater bei Drees & Sommer, ist überzeugt, dass „ein unterbrechungsfreier, digital kontrollierter und gleichmäßiger Straßenbau-Prozess – von der Asphaltanlage über die Lkw-Anlieferungen zum Beschicker und Fertiger sowie schließlich zu den Asphaltwalzen – zu einer flächendeckend guten Qualität und damit zu Straßen führt, die weitaus länger halten als bisher“. Doch wenn so viele Anlagen, Maschinen und Menschen an einem solchen Prozess beteiligt sind und auch Wind und Wetter ihre Stolpersteine in den Weg legen, muss man sich natürlich erst aufeinander einspielen – das Pilotprojekt war eine gute Gelegenheit.
Denn der Schlüssel für die Wirtschaftlichkeit einer Baustelle liegt in der Stabilität. Wie voneinander abhängige und interagierende Wertschöpfungsketten aus den Bereichen Baumaschinen, Baustellenumgebung, Baustellennetze und Bauprozessüberwachung zusammengeführt und vernetzt werden, um im gleichen Takt zu laufen. Und ganz praktisch auch darin, wie die Temperatur des Asphalts über den gesamten Prozess im optimalen Bereich gehalten werden kann. Diese Vernetzung ist heute über intelligente Vermessungs-, Hardware-, Software- und Cloud-Lösungen möglich, wie sie etwa von Topcon geboten und implementiert werden. Sie ermöglichen dabei die Erfassung der Ausgangs- und das Setzen der Zielwerte, eine technisch stabile Maschinensteuerung sowie die laufende zentrale digitale Qualitätssteuerung und ein effizientes Online-Monitoring der gesamten Baustelle.
Faktor 1: Bestandsdatenerfassung und Planung. Eine detaillierte Erfassung der Ausgangslage und exakte Planung und Projektierung sind das Fundament, auf der später die qualitative Ausführung fußt. Anstelle stundenlanger Querschnittsmessungen des Straßenbestands tritt heute der schnelle 3D-Scan. Der dafür notwendige RD-M1-Scanner von Topcon wird einfach auf ein Fahrzeug montiert und kann bei Geschwindigkeiten bis 100 km/h die Fahrbahnoberfläche erfassen, ohne Fahrspuren sperren zu müssen. Die Daten fließen in die von Topcon entwickelte Magnet-Software und werden dort zu großen Punktwolken und letztlich zu einem Modell der Fahrbahn verdichtet. Quer- und Längsneigungen sowie Verformungen können damit beurteilt werden. So zeigte im vorliegenden Projekt der Scan der Teststrecke eine starke Spurrillenformung und einen gesenkten Bereich, den es auszugleichen galt. Der bestehende Fahrbahnaufbau wurde zusätzlich über Georadar, Bohrkerne und Rammsondierungen analysiert. Das gibt Auskunft über die Schichtdicken und den technischen Zustand und zeigt, welche Schichten erneuert werden müssen.
Für die Vernetzung einer solchen Baustelle braucht es jedoch ein ausreichendes Daten-Funknetz, ohne das eine digitale Vernetzung der Maschinen und Kontrollmechanismen nicht möglich ist. Messungen auf der Teststrecke ergaben täglich, mitunter sogar stündlich wechselnde Verfügbarkeiten der Funknetze, was die Arbeit sehr erschwerte. Zur Absicherung des Datenempfangs wurde für alle Projektabschnitte ein eigenes WLAN-Netz aufgebaut.
Faktor 2: dynamische Logistiksteuerung. Um den Gesamtprozess kontrollieren und von zentraler Stelle aus eingreifen zu können, müssen alle Maschinen und Anlagen digital vernetzt sein. Dr. Marcus Müller von der Uni Hohenheim erläutert auf der Testbaustelle ein Beispiel: „Gerade stehen die Lkw Schlange vor dem Beschicker. Die beiden Fertiger würden auf einer normalen Baustelle jetzt Gas geben. Aber das System meldet ihnen, dass sie ihre geringe Geschwindigkeit von 2,5 m/min. beibehalten sollen. Denn – was sie aus ihrer Position nicht erkennen können, was das System aber erkennt: Die Asphaltanlage kommt gerade mit der Verladung nicht nach, bei höherer Geschwindigkeit würde es in 40 Minuten zu einem Stillstand des Fertigers kommen.“
Ziel der dynamischen Logistiksteuerung ist die temperaturabhängige Verladung und unterbrechungsfreie Anlieferung des Mischguts. Dazu wurden laufend die Verladetemperaturen der einzelnen Ausbringungen aus der Asphaltanlage und die Fahrzeiten der Lkw beobachtet. Über eine individuelle dynamische Steuerung der Belade- und Ankunftszeiten der Lkw bei der Asphaltanlage und dynamische Geschwindigkeitsempfehlungen für die Fertiger wurden die Prozesse schließlich so synchronisiert, dass das Mischgut mit einer kontinuierlich gleichbleibenden Temperatur ausgebracht werden konnte. Das wiederum führte zu sehr guten Ergebnissen hinsichtlich Ebenheit und Schichtenverbund der Asphaltdecke.
Faktor 3: technisch stabile Maschinensteuerung. Um die Maschinen so minuziös miteinander in Takt zu halten, dabei planparallele Aufbauhorizonte und einen ebenen, gleichmäßig starken Schichtenaufbau von Binder und Decke zu erreichen, bedarf er einer technisch stabilen Steuerung der einzelnen Maschinen, einer Vernetzung aller Maschinen und der zentralen Digitalisierung der gesamten Logistikkette.
So zeigte sich auf der Teststrecke, dass bereits die Einhaltung der Ebenheit beim Aufbauhorizont entscheidend ist. Ziel war eine plane Ausgangsbasis zu erhalten, die den Aufbau einer konstanten Tragschicht ermöglicht. Topcon bietet dafür zwei Alternativen. Wo keine Satelliten sichtbar sind, hilft das Positionierungssystem mittels Tachymeter. Die Robotik-Totalstation sorgt sekundengenau dafür, dass Fräse, Schild oder Bohle exakt ausgerichtet sind. Wo Satelliten erreichbar sind, ist meist die RD-MC-Maschinensteuerung die bessere Wahl. Statt Tiefen einzustellen oder Werte von der Straße abzulesen, gibt hier ein 3D-Entwurfsmodell millimetergenau die Frästiefe vor. So können die eingesetzten Fräsen mit variabler Tiefe immer genau auf das richtige Sollmaß pro Durchlauf abtragen.
Durch das gesteuerte Fräsen war bereits ein zur künftigen Deckschicht paralleles Planum entstanden. Beim Einbau setzte man somit darauf, den Fertiger nicht 3D-gesteuert, sondern mit Ausgleichssteuerung zu fahren. Um darüber hinaus auch alternative technische Möglichkeiten zu demonstrieren, wurden Teilbereiche mit der Topcon-RD-MC-Fertigersteuerung eingebaut. Die Schichtstärke wurde dabei, begleitend zum Einbau, mit elektro-magnetischer Messung kontrolliert.
Faktor 4: Online-Controlling beim Verdichtungsprozess. Für eine gleichmäßige Verdichtung ist die flächendeckende Verdichtungskontrolle direkt beim Verdichtungsprozess ganz entscheidend. Die vier Ammann-Walzen ARP95 verfügen dafür über das herstellereigene Compaction-Expert-System ACEpro, ein automatisches Mess-, Kontroll- und Dokumentationssystem, das nicht nur misst und analysiert, sondern Amplitude und Frequenz entsprechend dem Verdichtungsgrad automatisch anpasst. Das auf allen Walzen installierte FDVK-System von Topcon (flächendeckende Verdichtungskontrolle) erfasste im laufenden Prozess Kenngrößen wie Überfahrtenanzahl, Steifigkeit und Temperatur. Die Topcon C-63-Maschinensteuerung übernahm all diese Daten, ermittelte die exakte GNSS-Position der einzelnen Walzen und zeigte positionsgenau die noch erforderlichen Überfahrten an. So konnte eine gleichmäßige Verdichtungsqualität erreicht werden- mit erheblichem Einfluss auf die Langlebigkeit der Straße. Und durch den Datenaustausch in Echtzeit konnten die nachfahrenden Walzenführer direkt erkennen, wie viele Überfahrten die voranfahrenden Maschinen bereits geleistet hatten.
Faktor 5: mobile Vernetzung des Gesamtprozesses. Die Intelligenz dieser Systeme zeigt sich in der digitalen Vernetzung aller gesammelten Daten und Informationen. Es würde wenig nutzen, wenn jede Walzen nur wüßte, was sie selbst gerade leistet oder bereits geleistet hat. Erst in der intelligenten Vernetzung aller Informationen in Echtzeit steckt der Erfolg der Qualitätsbaustelle 4.0: indem jede Maschine auch weiß, was die andere gerade tut oder getan hat und ihr eigenes Handeln darauf abstimmen kann.
Auch hier spielen Topcon-Systeme, ergänzt durch die mobilen Apps von Ceapoint, eine Hauptrolle. So wurden alle Maschine via GNSS miteinander verbunden und konnten Informationen senden, wo sie sich gerade befinden und in welche Richtung sie sich bewegen. Die Anzahl der Walzüberfahrten wurden für jede Einbauschicht durch Kontrollmessungen mit einer Troxler-Sonde bestimmt. Dieser Wert wurde auf den Walzen im Topcon-System hinterlegt, so dass die Walzenführer durch entsprechende farbliche Darstellung informiert wurden, wann sie die notwendigen Überfahrten erreicht hatten.
Die Eingaben in die Cloud erfolgten dabei alle 30 Sekunden und nahezu automatisch. Im Laufe des Forschungsprojektes wurden auch alle Schnittstellen-Hürden erfolgreich gemeistert. Über einfache und intuitiv bedienbare Apps konnten die zentralen Informationen von allen Beteiligten auch bequem über Smartphone abgerufen werden. Um vor einer Informationsüberflutung zu schützen, konnte jeder nur die Informationen sehen, die ihn auch direkt betrafen.
Neben vielen kleinen Problemen, die während der Testphase gelöst werden konnten, gab es ganz konkrete Erfolge. So hat es das Team mehrfach geschafft, kontinuierlich acht Stunden ohne wartende Lkw oder stillstehende Fertiger einzubauen. Als zentraler Treiber fungierte der Fertiger, der seine Geschwindigkeit je nach Ansage des Systems drosselte oder erhöhte. Die Qualität der Asphaltdecken wurde nach jeder Einbauschicht flächendeckend über die gesamte Straße hinweg kontrolliert – und nicht nur linienweise mit dem Planografen, wie es die ZTV verlangt. „Wir konnten hier 7 km Straße mit digital vernetzten Maschinen in einer sehr hohen Qualität einbauen, die viele Jahre Bestand haben wird“, resümiert Raimo Vollstädt von Topcon. Noch ist der Aufwand einer solchen digitalen Baustelle recht hoch. Aber bis 2020 soll diese Art der Baustelle in Baden-Württemberg die Regel sein. Aktuell empfiehlt das Verkehrsministerium, je eine Landstraße pro Regierungspräsidium in dieser Bauweise umzusetzen.